CASE STUDY
PowerCom Empowers Technicians with LinkWare™ Live to Increase Team Efficiency
Download PDF
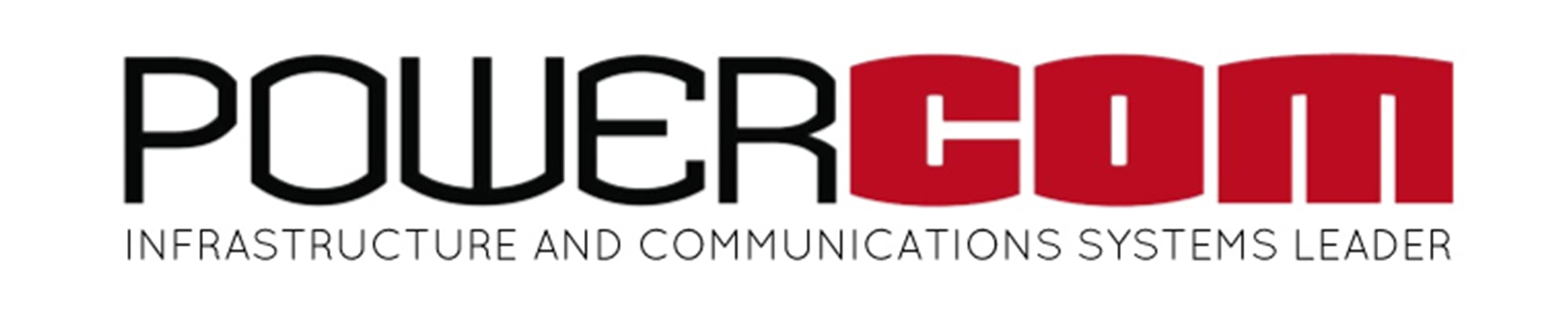
At a Glance
Customer: PowerCOM
Industry: Information and Communications Systems
Location: Bothell, WA
Challenge:
PowerCOM installs and services a wide range of information and communication systems including; voice, data, Wi-Fi, security and monitoring at a variety of both indoor and outdoor locations. With over 80% of employees working in the field on multiple client sites, delivery of test results to the PowerCOM office and/or client is often challenging. Historically, the process to set up test equipment and compile results has been manual and time intensive for both field and administrative staff. Additionally, some customers desired more frequent and periodic delivery of detailed test results, rather than only upon project completion. To address these issues, PowerCOM required a solution that could help their technicians and administrative staff be more efficient, as well as readily and more easily share data with their customers.
Result:
By leveraging Versiv™ DSX-5000, CertiFiber® Pro and LinkWare™ Live, PowerCom has significantly reduced the time and effort needed to test the systems and provide results to their customers. Instead of requiring the field technicians to set-up test parameters and commute to the office to deliver/review the test reports, these tasks can be done remotely through the cloud. By leveraging LinkWare Live, PowerCom technicians can complete jobs faster, ensure test accuracy and reduce the potential for rework.
Product:
LinkWare™ Live with Versiv DSX-5000 and CertiFiber Pro
On This Page
Overview
Headquartered in Bothell, WA, PowerCOM provides telecommunications and network services to its customers. With over 80 employees supporting two offices, PowerCOM strives to deliver the highest-quality service within defined time frames for every job. Each month, PowerCOM completes many jobs across multiple clients and it is common that a single project might require multiple staff to complete hundreds or thousands of tests.
In an effort to maximize efficiency, PowerCOM attempts to limit “non-productive” testing time which could include driving back-and-forth to the corporate office or manually compiling results to verify testing parameters. This non-productive time adds overhead, costs and delays for each job.
Challenges
PowerCom wanted to find new ways to become more efficient without sacrificing quality. They knew the key was to look for ways to: save technicians’ time, improve test accuracy and validation, and streamline the customer experience. With this in mind, there were three main processes they identified that could be improved to positively impact their service, delivery, and bottom-line:
Configuration of test parameters: Previously, an experienced manager or technician would need to configure the test parameters on each device prior to starting a new job. However, this was a manual process, which was time intensive and required unproductive travel time to bring the device into the office from the field. Letting the testing experts perform this critical process remotely would save technician’s time (not to mention vehicle wear and tear) while guaranteeing consistent testing.
Early test validation: Test accuracy is always a concern because improper testing means wasted time and rework. In situations when deviations or invalid tests are not quickly identified, it could require the technician to return to the project later to repeat the tests, causing delays and increased expense.
Data retrieval: Once the tests are completed, additional time was required to drive or ship the results to the office, and then upload results to their computer. To complicate things, naming conventions and documentation could overlap which can cause discrepancies. And with multiple testers on multiple projects, getting the right tests into the right job took a lot of time. In the past, this process typically occurred at the end of the project, however, customers increasingly desire updates throughout the project. PowerCom wanted to simplify this time-consuming and error-prone process, while also meeting new customer expectations.
““The biggest value of LinkWare Live is that test parameters can be set up in one central point and transmitted via the cloud by both technicians and administrative staff. We’ve eliminated the drives to and from the office specific to test reporting which has resulted in more accurate reporting and faster project close-out.””
CJ Santeford, Operations Manager of PowerCom
Solution
After purchasing the Fluke Networks copper and fiber testers (DSX-5000 and CertiFiber Pro) Powercom decided to leverage the LinkWare Live companion cloud-based platform as part of their testing workflow in an effort to save time, meet growing customer expectations, and ensure more accurate testing.
Results
Using the Versiv testers in conjunction with LinkWare Live, the PowerCom team has improved overall testing experience, shortened completion times and increased efficiency of field technicians, project managers and administrative staff. By passing the time and cost savings to its clients, PowerCom turns this to a competitive advantage.
“Before LinkWare Live, our field technicians had to come into the office or send their testers in for downloading or configuration.” said CJ Santeford, PowerCom Operations Manager. “But now, we can download and configure through the cloud which saves us a ton of time. At a minimum, we save an hour per week of technician time related to these common tasks.”
Sharing and saving test results has become much easier as well. The cloud-based LinkWare Live allows technicians to sync data remotely and let the system compile results. “Without LinkWare Live, it was a painful and time consuming process to manually organize results. It is now much easier and faster to pull in accurate results for each job,” stated Santeford. “Our service and support team can also provide customers with direct access to the results through the intuitive user interface.”
“This is helpful for our customers who want access the test results throughout the duration of a project”, commented Santeford. “For our field techs, the test parameters and identification numbering is already set up and saved to the tester. The field tech simply finds the project in the directory, and hits a button to perform the test based on the preconfigured labeling scheme. It's intuitive and very easy to use.”
“The biggest value of LinkWare Live and Fluke Networks is that test parameters can be set up in one central point and transmitted via the cloud by both technicians and administrative staff.“ concluded Santeford. “We've eliminated the drives to and from the office specific to test reporting which has resulted in more accurate reporting and faster project closeout. Using LinkWare Live has definitely impacted our time savings, which translates to a cost savings for our customers – the true win/win scenario.”